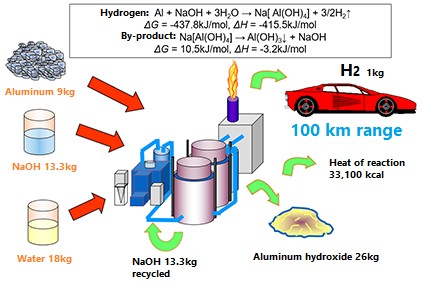
Green hydrogen manufacturing system Hydrogen production system from waste aluminum and silicon
Green hydrogen is an environmentally friendly system that does not use fossil fuels. Our system produces hydrogen by reacting aluminum (aluminum dross and other waste aluminum from the aluminum melting process) and silicon (waste silicon from semiconductor wafer shavings) with an alkaline solution. This process is being researched and developed worldwide because of its usefulness in bringing about a hydrogen energy system society.
Green hydrogen manufacturing system – Prototype
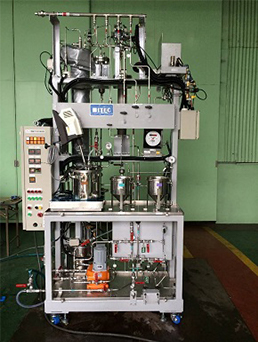
This is a prototype system that continuously reacts waste aluminum and waste silicon slurry with alkaline solution to produce hydrogen. This system will be used as a test system for scale-up to mass production. The apparatus records changes in slurry supply rate, temperature, pressure, and hydrogen flow rate over time. This is useful for optimizing reaction conditions.
Flow diagram
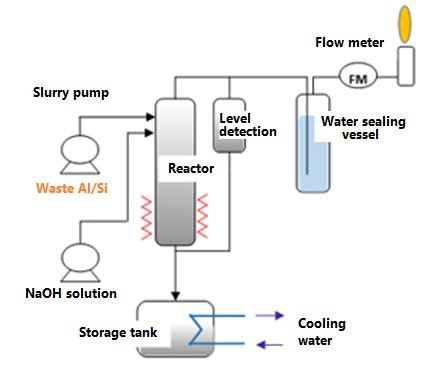
Videos
Specifications (operational record)
Design Pressure | 0.1MPa (Operation: 5 kPa) |
Design temperature | 100℃ (Operation: ~60℃) |
Volume of vessel | 10L |
Slurry feeding rate | 200ml/min (~30wt%) |
NaOH feeding rate | 70ml/min (8 mol/L) |
Hydrogen flow rate | ~820L/Hr (with NH3) |
Reaction time | ~40 min (Al 18.3wt%. AlN 3.3wt%) |
Volume of slurry tank | 10L(with agitator) |
Volume of NaOH tank | 4L |
Volume of cleaning water tank | 4L |
Volume of waste liquid tank | 20L (continuous discharge is available) |
Cooling capacity | 1100W (water 20℃) |
Size | 1500Wx850Dx2600H |
Green hydrogen manufacturing system – Skeleton type
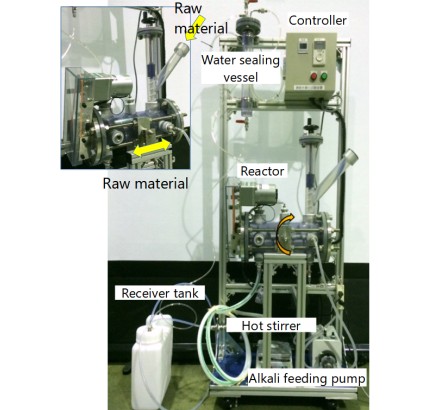
This is a skeleton type test system that continuously reacts waste aluminum and waste silicon slurry with alkaline solution to produce hydrogen. The reactor is transparent and has an adjustable tilt. The fed material is continuously conveyed by a screw. The produced hydrogen is led to a water-sealed tank, which is closed off from the outside air, so the reaction can be safely observed. By installing a flow meter (optional), the amount of hydrogen produced can also be measured.
Flow diagram
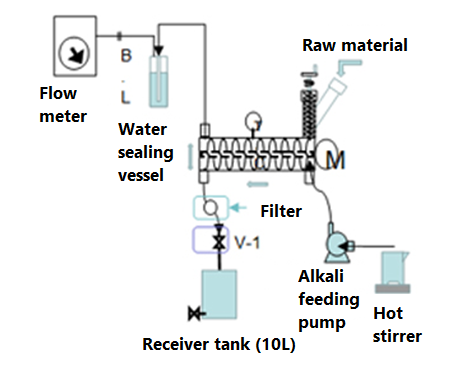
Videos
Size of reactor | inner diameter 126mm, length 400mm |
Screw pitch | 50mm |
Screw rotation speed | 0.15~2.65rpm |
Feed speed | 7.5~132.5mm/min |
Reaction time | 3.0~53min |
Reactor material | PVC, SUS304 |
Water seal tank material | PVC |
Power supply | AC 100V |
Green hydrogen manufacturing system – Batch type
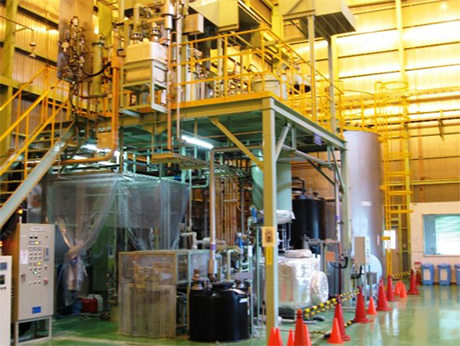
This is a large system that reacts waste aluminum and waste silicon slurry with alkaline solution to produce hydrogen. Ammonia generated at the same time is separated by a scrubber. Ammonia can be converted to hydrogen by low-temperature decomposition. This system can also be applied to waste treatment such as waste silicon.
Example of facility
Throughput | almidross 100kg/batch |
Hydrogen production | 37.3m3/batch 6.6ton/year at 30.84% of metal |
Size | 4600Wx15100Lx8300H |
Flow diagram
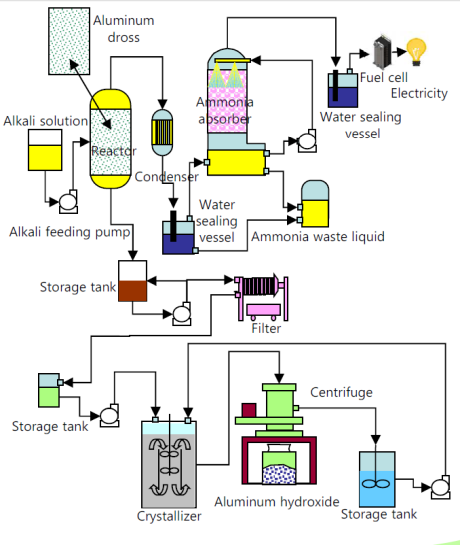
Characteristics
- Hydrogen can be used for fuel cells by refining.
- Sodium hydroxide can be reused in the crystallization process.
- By-products are aluminum hydroxide (used in crystallizer) and sodium aluminate (raw material for zeolite).
- Ammonia gas can be removed by scrubbers or converted to hydrogen by low-temperature decomposition.
- Metallic aluminum and aluminum nitride in waste aluminum are completely decomposed.
- The purity of the byproduct aluminum hydroxide is 99% (measured value).
- Residue after the reaction can be washed with water to meet effluent regulations.